カイゼンとBPM ~業務プロセスを可視化することはムダなのでしょうか?~
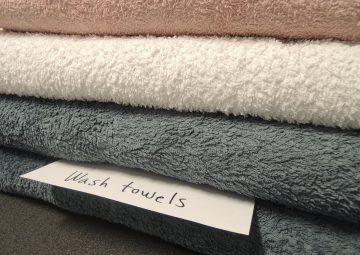
カイゼン
業務プロセスの改善に興味のない経営者はいないでしょう。トヨタ生産システムは生産現場の改善手法のお手本として世界中の企業で研究されています。海外の他の優れた手法とも融合し、生産現場以外も含めたあらゆる分野に適用され、今日でも日々進化しています。IT分野でも「アジャイル開発とカイゼン」などというテーマはまだまだホットですね。業務プロセスの可視化・維持管理手法であるBPM(ビジネスプロセスマネジメント)ももちろん無縁ではありません。本稿ではカイゼンとBPM、両者の共通点と違いを整理し、業務プロセスの改善がなかなかうまく進まないお客様に対して1つ提言したいと思います。なお、文中では「カイゼン」はトヨタの思想・概念、「改善」は一般用語として区別します。
パソコン上の改善と現場のカイゼン
BPM とは「業務プロセスのPDCAサイクルを回して業務の成果を上げる事」(日本BPM協会様 Webページより)です。一言で言えば業務改善の仕組みです。こう説明すると、特に生産管理に触れたことのある方からは、現場のムダ取り手法を想像されてしまうことがあります。しかし、BPMは欧米生まれのトップダウンな管理手法として誕生したこともあり、現場の現状を起点とするボトムアップな改善について特別な方法論を持っている訳ではありません。欧米には性悪説がベースにあり、現場が自ら気づいて改善し続けるような事をそもそも期待していません。BPMのアプローチでは、少数精鋭の幹部が事業戦略に沿って標準プロセスを机上で設計し、それを現場に展開して徹底的に守らせます。まずはガバナンスに主眼を置き、改善検討は標準プロセスのパフォーマンスを測るKPIの値を見て行われます。もっと良くするために施策を立案し、標準プロセスが修正され、改めてトップダウンで現場へ展開します。このように標準プロセスの展開と改善をPDCAサイクルの中で繰り返し、企業全体の底上げをしていくことをBPMでは「継続的改善」と呼んでいます。
次にトヨタ方式を見ていきます。同様に標準プロセスを作り、これをさらに改善してスパイラルを回すという点では共通です。しかし、そのやり方においてはITやツールに頼らず、組織と人が現場で回しているという点が1番の特徴だと私は考えています。トヨタのカイゼンは現場の人がリアルにやっています。現地現物を対象としてリアルタイムに問題解決しています。現場が自律的に改善してゆくための思想、仕組み、テクニックが揃えられています。その詳しい内容は世のたくさんの書籍に解説されていますので本稿での論説は避けますが、本稿で対比したいポイントは「どこに標準プロセスのマスタ(原本)があるか?」です。BPMでは標準プロセスをパソコン上にモデル化し、これをマスタとします。トヨタの標準プロセスのマスタは現場そのものです。現場をそのままダイレクトに改善しようとします。BPMではパソコン上の標準プロセスが現実と乖離していないかをいちいち確認した上で改善を検討し、改善案を改めて現場に徹底しなければならないという点を考えると、トヨタ方式の方がスピード感のあるやり方であり、効率的であることも明らかです。どうしてそんな事が可能なのか、もう少し踏み込んでみます。
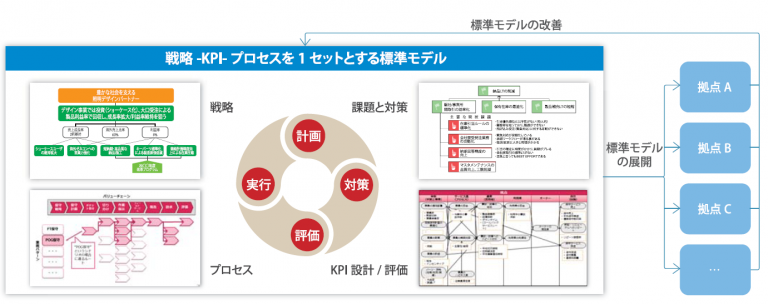
(図1:BPMの継続的改善サイクル)
見える化
トヨタ流の「問題の見える化」について触れてみます。トヨタではパソコンの画面を睨まないと問題が見えてこないような状態のことを「見える化」とは言いません。「見える化」とは現場を見渡せば問題が目に飛び込んでくるくらいの状態の事を指します。その前提には仕事の「流れ化」があります。仕事が標準に従って淀みなく流れているからこそ、標準とは異なる事象(淀み)にすぐ気づくことができる、かつ、目に飛び込んでくる。これが「見える化」です。トヨタのモノづくりの現場では、改善ワークショップで一時的に「価値と情報の流れ図」というものを紙に描くことはありますが、BPM で推奨するように業務プロセスを恒常的にモデル化し維持管理するようなことは行われていないそうです。なぜなら、現場の管理職の頭に入っているため、正常時に現場で何が行われているかがしっかり分かっているからです。問題が起きた時には即座に異常に気づき、その時点でラインを止めて問題解決をします。現地・現物を対象に、リアルタイムにプロセスマネジメントができている状態であると言えます。このような状態にあってこそ、現場主導の自律的な改善が成り立つのです。
それができないから
残念ながらお客様のほとんどの職場はこの境地には至ってはいません。正常時に現場で何が行われているのかさえ、正確にはわかっていないのが実情です。一朝一夕にトヨタのようにはなれませんので、まずは現場のプロセスに責任を持つ方を決め、現場の現状プロセスを理解させることが先決です。そのために業務プロセスをモデル化するという事をBPMは推奨します。現場の業務プロセスを理解していなければ、課題を俯瞰し正しい解決策を打つことなどできないと信じているからです。ただし、モデル化するという事は現実を抽象化するという事です。現地・現物に比較すると情報は劣化します。モデル化した瞬間から陳腐化も始まります。トヨタに言わせれば、モデルを書いて維持管理するというムダが生じることになります。悩ましいですね。
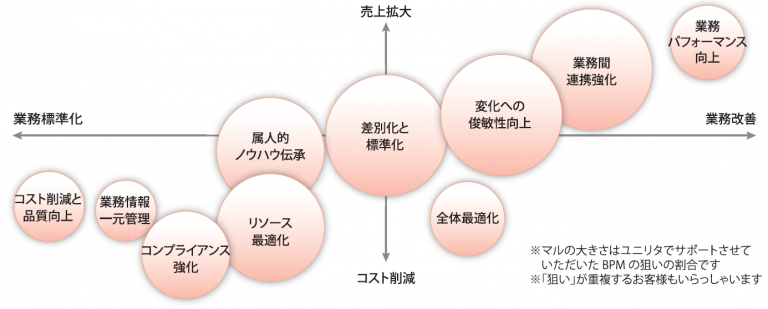
(図2: 業務プロセス可視化の狙い)
最近、私も少し勉強して目から鱗だった事があります。トヨタでは7つのムダを規定して徹底的にそれらを排除することが原則だと理解していました。ムダな事は絶対にやらない人達なのだと。ところが、その原則の土台になっているもっと重要な信念があるそうです。それは「長期的な考え方」というものです。短期的な財務目標を犠牲にしてでも、長期的な考えで物事を判断するという事です。長期的にムダを排除するためなら、ある程度の短期的なムダは敢えて作り込むそうです。これもまた、簡単には真似できそうにありませんが、業務プロセスの可視化と維持管理、さまざまな社内のステークホルダに問題を理解させるため、短期的なムダと捉えてみるのも良いかもしれません。